No rain today, so I managed to get a far bit of progress made on the forms for the rammed earth wall.
My design for these is changing almost weekly, but I think I’ve finally arrived at a final prototype. The columns are pretty much done, with only one set of chamfers and a control joint tongue to cut. The side panels however are going to take quite a lot longer to put together…
The thing I love about working with timber is the instant gratification. It doesn’t take much effort or time to cut the timber to precise length, and screw / nail / glue it together and bam, you’ve built something.
Maybe I’m just new at it, but working with steel is just a pain in the arse in comparison. Firstly, I’m finding it a lot harder to cut the steel with anywhere near the same level of precision. Granted that’s probably my choice of tools (a GMC chop saw and Ozito angle grinder) but putting that aside it takes much longer to cut. I spent all morning just cutting up the 50x50x5 steel angle to length.
Then, once the steel is cut it has to be assembled which means welding. Now, I know I’m a rank amateur with the oxy torch, but still this takes forever! Nothing as simple as drilling a clearance hole and screwing in a tek screw or coach bolt.. there’s the initial tack welding assembly, then going back and butt or seam welding the pieces together. And then it’s inevitable that I’m going to have stuffed something up, but I can’t just unscrew that bit and adjust it; the welds have to be ground off (if you can get at them) and … see, it even takes an age just to describe how long it takes to work with steel!
Then there’s the mess and the sparks and the burns and the smell…
Anyway.
I managed to get one form panel finished, and the steel for a second cut to size. I have however been short changed one bottle of acetylene - I suspected as much the first time I used it, the pressure in the tank was lower than it should have been and the bottle was supplied without a protective cap. Sure enough, I’m out of acetylene and I still have 90% of a full tank of oxygen. Bugger.. that put a stop to the day’s progress.
Here’s what I did manage to get done:

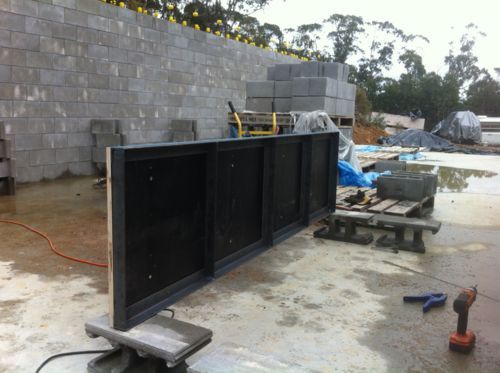
So that’s one down, at least three to go. I may need to build more, if it turns out that I can’t leapfrog the lower panel up above the one I’m ramming against. Wonderful, I’m looking forward to it already…
I am glad I decided to build these smaller than I’d first intended - it was a challenge moving this panel into the container, let alone lifting it up 1.8m into the sky. It does seem plenty strong enough though - I can stand on the middle of the panel and it doesn’t bend much if at all, which bodes well for straight rammed earth walls!
(I did notice however that these will make fine work benchtops for the garage when I’m finally finished with them :) That’s a silver lining, and I’m sticking to it!)